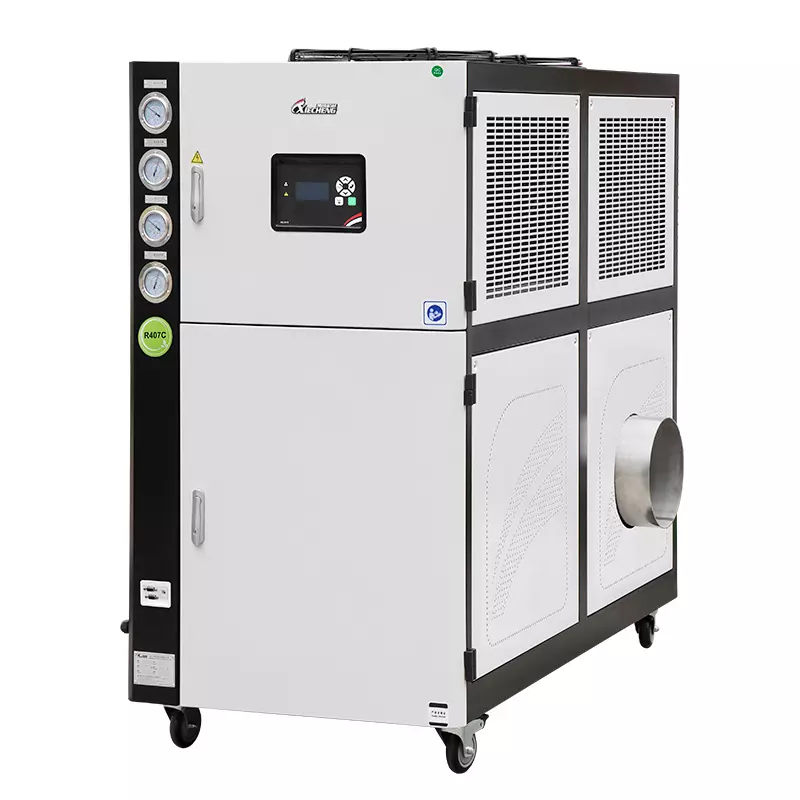
Product Description
Industrial Air Cooling Chamber
Industrial air cooling chamber provides low-temperature and dry air for the stable extrusion of blown film. Compared to traditional water chillers with heat exchanger systems, utilizing the direct expansion of refrigerants to cool the air can save energy. Regardless of environmental conditions, the air temperature provided by the air cooler matches the ambient temperature, which is crucial for plastic processing on blown film production lines.
Blown film technology is a commonly used method in contemporary industrial plastic processing. It involves heating plastic materials, such as PE particles, to a molten state, and then using high-pressure air to blow and shape them into thin films. The films are subsequently cooled and solidified with cold air. These high-quality packaging films, applied in various industries including fresh produce, beverages, and pharmaceuticals, result from this process.
In the production process of blown film machines, precise temperature control is paramount, especially during the film forming stage. The quality of the films is significantly influenced by the cold air used for cooling during shaping. Both excessive and insufficient cooling rates can lead to issues like poor transparency, uneven thickness, and variations in tensile strength. These problems not only affect production efficiency but also impact the quality of the films.
To address the challenges arising during the cooling and shaping phases of blown film technology, XIECHENG has introduced specialized air cooling chamber for blown film machines. These coolers are designed to substantially enhance both cooling production efficiency and film quality.
① | Compressor | ⑤ | Finned Evaporator |
② | Finned Condenser | ⑥ | Blower Fan |
③ | Dryer Filter | ⑦ | Defrost Solenoid Valve |
④ | Expansion Valve | ⑧ | Refrigerant Solenoid Valve |
| Feature:
The specialized air cooling chamber for blown film machines is a refrigeration equipment developed and produced by manufacturers according to the production requirements of blown film technology. It can provide stable cold air ranging from 5 to 30°C, aiding in rapid cooling during the process forming stage. This helps reduce production cycles, enhance efficiency, and ensure the quality of blown film.
1. Strong refrigeration capacity, low noise, and energy-saving characteristics.
2. Full-function microcomputer control with LCD display for simple and intuitive operation.
3. Inlet designed with a filter device for easy maintenance and cleaning.
4. Equipped with automatic defrosting function to effectively reduce energy consumption.
5. LCD screen displays both cold air outlet temperature and equipment-set temperature.
6. Comprehensive safety protection features and an intuitive display system for abnormal conditions.
| Specifications
Model |
UNIT |
XC-LF5AF |
XC-LF10AF |
XC-LF15AF |
XC-LF20AF |
XC-LF25AF |
XC-LF30AF |
|
Motor |
HP |
5 |
10 |
15 |
20 |
25 |
30 |
|
Refrigerating Capacity |
KW |
15 |
31 |
45 |
61 |
68 |
92 |
|
Kcal/h |
12900 |
26660 |
38700 |
52460 |
58480 |
79120 |
||
Temperature of Air Outket Control |
℃ |
8-15℃ |
||||||
Input Power |
380V 50HZ 3PH |
|||||||
Conpressor Power |
KW |
3.7 |
3.7*2 |
3.7*3 |
7.5*2 |
9*2 |
7.5*3 |
|
Cooling Refrigerant |
R22(Optional for R410C, R407C) |
|||||||
Condenser |
Type |
air cooled type |
||||||
Air Flow |
m3/hr |
2100 |
3000 |
4800 |
4800 |
6000 |
6000 |
|
Fan Power |
KW |
2.2 |
3.75 |
11 |
11 |
15 |
15 |
|
Air Connection Pipe Diameter |
inch |
10'' |
10'' |
12'' |
12'' |
12'' |
12'' |
|
Evaporator |
Type |
Copper tube jacket corrugated open window aluminum foil fin radiator, outlet temperature will be lower |
||||||
Dimensions(L*W*H) |
L |
mm |
1340 |
1550 |
1850 |
2150 |
2400 |
2600 |
W |
mm |
630 |
830 |
1000 |
1000 |
1150 |
1150 |
|
H |
mm |
1046 |
1508 |
1600 |
1780 |
1800 |
1900 |
|
Safety Protection |
High and Low Pressure Protection, Overload Protection,Overtemperature Protection, Phase Sequence Protection,etc. |
| Product Details